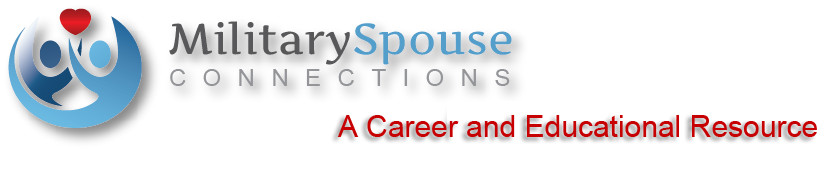
Job Information
Ford Motor Company Design Industrialization Engineering in Raleigh, North Carolina
At Ford Motor Company, we believe freedom of movement drives human progress. We also believe in providing you with the freedom to define and realize your dreams! With our incredible plans for the future of mobility, we have a wide variety of opportunities for you to accelerate your career potential as you help us define tomorrow’s transportation. Ford Model E is responsible for developing the key technologies and capabilities – such as EV platforms, batteries, e-motors, inverters, charging and recycling – to create ground-up breakthrough electric vehicles. By joining the best software, engineering, design and UX talent, you will be a part of creating innovative technologies and concepts that can be applied across the Ford enterprise. Being on the Ford Model E team means building the future as Ford’s center of innovation and growth through electric and connected vehicles and services.
The Design Industrialization Engineer will drive cross-functional collaboration between product development, supply chain, manufacturing, and external suppliers to ensure alignment on requirements, provide critical feedback on part designs, 2-D drawings, and directly improve specification development procedures for Ford’s next generation electric powertrains.
*What you will be able to do: *
Supplier Industrialization
- Own processes, supplier communication, and documentation from concept-stage sourcing activities through mass production, including the transition from start of production up to high volume production with new and existing suppliers. This includes PPAP of sourced components.
Sourcing Phases:
Define supplier quality goals for prototype and pre-production activities and drive reliability goals using FMEA and DFM tools.
Evaluate supplier capabilities using Product DFM and Process DFM tools with the goal of selecting the most suitable supplier and proactively manage supplier risk.
Audit new suppliers, assess capabilities and cultural fit.
Direct suppliers to quote and develop innovative production solutions to achieve industry leading product quality, capacity at lowest cost.
Be a key player in the definition of machines, tooling, and inspection equipment to industrialize the most suitable process with the goal to meet all product specifications.
Be a key contributor to business award decisions with a focus on industrialization and quality.
Design Industrialization
Support the engineering team in the development of requirements and specifications with the goal of optimizing product cost, capacity, and supplier industrialization timing for parts and products sourced globally.
Support the engineering and product design team with the preparation and checking of 2-D drawings, GD&T, and component specifications.
Production Phases and PPAP
Define part-specific PPAP requirements.
Lead suppliers through prototype, pre-production, and safe launch PPAP phases as the responsible owner of sourced supplier sites, process control and quality documentation approvals.
Lead process and equipment validation, capability analysis, and PPAP approvals for the tiered supply chain (tier 1 to tier n) with the goal to meet quality goals, capacity targets and milestones.
Lead and conduct supplier visits to ensure accuracy of information, audit new suppliers, and approve PPAPs. Lead new product introduction activities with new and existing suppliers.
Support the manufacturing and quality teams to resolve supplier part quality issues through root cause analysis, corrective and preventative actions.
Cost-Driven DIE Involvement
Support the Global Supply Management (GSM) team during commercial negotiations, should cost analysis, and product cost optimizations with supplier process, manufacturing, quality, and equipment details to ensure quoted costs meets reality of production.
Support the cross-functional team to ensure the costed bill of process is accurate, complete, and aligns with the supplier industrialization requirements.
Drive lean manufacturing methods, identify areas for future cost improvements and waste reductions in all areas.
Ability to provide feedback on supplier processes to ensure manufacturability and cost optimization.
*The minimum requirements we seek: *
B.S. in Mechanical, Electrical Engineering or related field
5+ years’ experience in a personal contributor role in automotive supplier quality, production, or manufacturing environment.
In depth understanding of PPAP, APQP, GD&T, DFM, and Root Cause Analysis, Failure Mode Avoidance and Process Controls
Understanding of QMS, MSA, SPC, Lean Six Sigma, and SPC software (Minitab)
Effective communication skills for working with a global supply base
Expected domestic and international travel 30-50%
*Preferred Requirements: *
Strong engineering and quality skills to support supplier process and quality negotiations
Previous experience as a design and quality engineer
What you will receive in return:
As part of the Ford family, you will enjoy excellent compensation and a comprehensive benefits package that includes generous PTO, retirement, savings and stock investment plans, incentive compensation and much more. You will also experience exciting opportunities for professional and personal growth and recognition. If you have what it takes to help us redefine the future of mobility, we would love to have you join us.
Candidates for positions with Ford Motor Company must be legally authorized to work in the United States. Verification of employment eligibility will be required at the time of hire. Visa sponsorship is available for this position. We are an Equal Opportunity Employer committed to a culturally diverse workforce. All qualified applicants will receive consideration for employment without regard to race, religion, color, age, sex, national origin, sexual orientation, gender identity, disability status or protected veteran status.
For information on Ford's salary and benefits, please visit: https://corporate.ford.com/content/dam/corporate/us/en-us/documents/careers/2021-benefits-and-comp-LL6-sal-plan-2.pdf At Ford, the health and safety of our employees is our top priority. Vaccination has been proven to play a critical role in combatting COVID-19. As a result, Ford has made the decision to require U.S. salaried employees to be fully vaccinated against COVID-19, unless employees require an accommodation for religious or medical reasons. Being fully vaccinated means that an individual is at least two weeks past their final dose of an authorized COVID-19 vaccine regimen. As a condition of employment, newly hired employees will be required to provide proof of their COVID-19 vaccination or an approved medical or religious exemption.
Requisition ID : 34650
Ford Motor Company
-
- Ford Motor Company Jobs