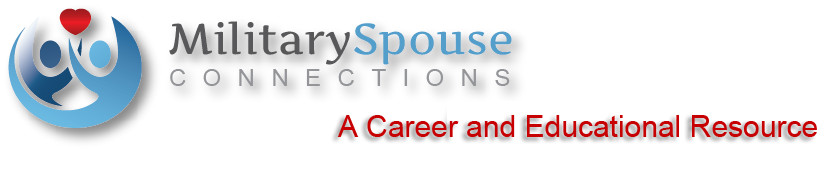
Job Information
Tennant Company Senior Engineering Test Technician in Golden Valley, Minnesota
Senior Engineering Test Technician
With more than $1B in revenue, Tennant Company is a globally recognized leader in the cleaning equipment industry. For the past 150 years, we have been passionate about developing and manufacturing innovative and sustainable solutions for our customers. At Tennant Company, we are committed to stewardship and creating a cleaner, safer and healthier world. With manufacturing, operations and sales, service, and support functions across the globe, your journey at Tennant can take you places you never expected.
PURPOSE/SCOPE:
The Sr. Test Technician plays a crucial role supporting engineering in developing & validating, systems, including machinery, components, automated equipment, electrical, software, hydraulic and robotic systems. The Sr. Test Technician provides expert direction in equipment selection, setup, troubleshooting, and repair of production test equipment/ fixtures (automation control panels, PLCs, AC/DC drives, programmable relays, timers, contactors, relays, motors, and pneumatics cylinder/valves).
GENERAL RESPONSIBILITIES:
Perform experiments and tests on a variety of projects as assigned by engineering supervisor.
Participate as required within R&D on various engineering efforts for new product development and current product improvements.
Assist in the generation of documentation (i.e. drawings, specs, procedures, work orders etc) required to support new product development projects.
Plan, build, conduct, and monitor all standard and complex tests, including the development of automated accelerated system and component endurance tests
Validate, troubleshoot and repair electrical, software, robotic, automated and hydraulic systems.
Use soldering equipment and handtools to install electronic parts, hardware, and instrumentation
Use instruments to test the performance of electromechanical assemblies
Drive a variety of machines including PIT’s, current products, and prototype equipment.
Verify dimensions of parts, using precision measuring instruments
Read engineering drawings, schematics, and diagrams for prototype and production parts to determine the method and sequence of assembly or repair of a machine or a piece of equipment
Uses technical capability and significant problem analysis to establish most effective solution for complex problems that involve interaction of several technical disciplines.
Assists in other areas of the Product Development Lab as the work load changes.
Monitor active testing for signs of failure or problems
Mentor, instruct, and develop less experienced Technicians and temporary employees
Troubleshoot and suggest creative solutions to design and testing issues.
Coordinate and execute building of prototypes/products per engineering design and instruction as required.
Perform standard testing processes on a variety of equipment and record and analyze results.
Record data from testing in standard formats and provides results to product and engineering teams.
Assists technical teams with recommendations to resolve testing problems, roadblocks or equipment malfunctions that impact the performance or validity of testing.
Requires knowledge and experience using CAN tools for recording and decoding messages on vehicle CAN bus.
Performs in-process inspection of products with use of standard and specialized inspection equipment.
Work overtime as required to support Production operations.
Perform gage verification & calibration efforts as necessary.
Work with engineering on build/test fixturing.
Understanding of and ability to utilize electronic data collection systems and computer software packages to collect and analyze data using basic statistics.
Working knowledge of Programmable Logic Controls (PLC) and User Interfaces (UI) as well as the programming environments for them
Working knowledge of National Instruments Labview environment
Apply Strain Gauges, Pressure Transducers, Thermocouples, Flow Sensors, Load Cells, and other instrumentation
Ability to prioritize work by determining the sequencing and timing of different jobs based on precedence and importance.
Follow safety guidelines and utilize appropriate safety devices when performing all tasks that require such precautions.
Create and Maintain accurate records to recreate desired build processes and designs.
Willingness for active participation, active listening, interpreting, cooperation and flexibility to allow for a successful self-managed team.
Be able to clearly communicate ideas, problems and solutions to engineers.
Support all Company initiatives as identified by management and in support of Quality Management Systems (QMS), Environmental Management Systems (EMS), and other regulatory requirements.
Complies with OSHA, other regulatory requirements, Company policies, operating procedures, processes, and task assignments. Maintains positive and cooperative communications and collaboration with all levels of employees, customers, contractors, and vendors.
REQUIRED EXPERIENCE & EDUCATION:
Two years trade school or one year trade school and one year college
10 years of related experience.
Must be legally authorized to work in the United States without sponsorship
REQUIRED INTERPERSONAL & BEHAVIORAL SKILLS:
Ability to organize, work independently, communicate effectively and strong time management
Interacts with team members and peers to anticipate and resolve day to day issues and competing project priorities.
Develop ways to improve technical methodology, processes, and products.
Ability to solve complex technical problems using diagnostic tools, data, and sound reasoning.
Experience with hands-on electronics work. This includes debug, and build of circuitry, specialty cables, and other parts in a lab environment.
Electrical AC and DC
Understand the principles of electricity. To wire a variety of machines from electrical diagrams, schematics, or from general knowledge of how our machines function. To troubleshoot any problems that occur on Tennant machines in the proper sequence, including: wiring machines, reading diagrams and schematics.
Hardware - English & Metric
Ability to identify all hardware required to fasten joints on machines. This requires knowing size, length, and number of threads per inch, grade and style of hardware called out, as well as knowing metric hardware specifications.
Hydraulics
Understand the principles and use of Fluid Power. Includes proper hose selection, selection of fittings, routing hoses, proper port selections on pumps/valves from hydraulic schematics and diagrams. Use of first & second time TORQUE values on hoses/fittings, troubleshoot and repair the same. Hose Selection, Fittings, Torque Values, Troubleshoot, Hose Routing, Port Selection, Fabrication of Hoses, Hydraulic Schematic/Diagram, and Repair.
Inspection
Checking of all parts produced to make sure they meet all specified dimensions and tolerances according to the engineering drawing. This requires high level of skills in blueprint reading, the use of basic and advanced inspection equipment.
Torque Control
The knowledge to properly tighten all hardware used to secure parts to machines. This involves knowing the type of hardware, type of joint being secured, and torque required to hold that joint securely. Has to know which pneumatic torque gun and torque bar to use to tighten the hardware correctly.
Ability to provide positive constructive feedback to resolve design issues in NPD, Current Products and Custom Solutions. This is necessary in the development and implementation of innovative ideas.
Flexibility and willingness to handle a variety of tasks productively and effectively
Experience with mechanical assembly and metal fabrication.
Experience with SAP, MS Office – Word, Excel, etc.
Understand processes and products in multiple areas.
Knows components used in clamping and locating parts on jigs and fixtures, including fixture plumbing and hydraulic knowledge.
Checking of all parts produced to make sure they meet all specified dimensions and tolerances according to the engineering drawing. This requires high level of skills in blueprint reading, geometric tolerance, the use of basic inspection equipment, shop math, and finishes on machined parts.
Must be able to add, subtract, multiply, divide fractional and decimal numbers. Ability to convert fractions to decimals and decimals to fractions. Know how to use geometry and trigonometry in the figuring of angles.
Analyze and resolve manufacturing issues in various departments and help implement lean initiatives, process improvements and Safety.
REQUIRED PHYSICAL DEMANDS:
Routinely lifts up to 40 pounds individually
Works in multiple positions during a shift
Ability to stand for an 8 hour shift
May alternate between sitting and standing.
ENVIRONMENTAL EXPOSURES:
Routinely and regularly works near moving mechanical parts
Occasionally exposed to hot conditions
Occasionally exposed to non-toxic fumes
Moderate noise level
Occasionally exposed to oil, grease, fuel, dust, metal particles and sharp edged materials
SAFETY REQUIREMENTS:
Must be able to wear safety glasses, steel toed shoes and hearing protection
Necessary to follow established safety practices to avoid injuries in working with a variety of
hand and machine tools.
Begin your journey with us. Let's reinvent how the world cleans.
Equal Opportunity Employer
Tennant Company is an equal opportunity employer. Employment decisions are made on the basis of individual skill, ability, reliability, productivity, and other factors important to performance. We do not discriminate on the basis of race, color, creed, religion, sex, national origin, physical or mental disability, age, veteran status, pregnancy, sexual orientation, genetic information, gender identity, or any other basis protected by state or federal law or local ordinance.