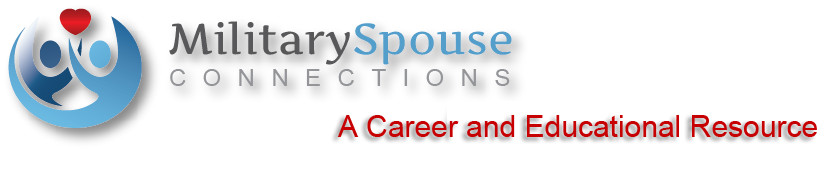
Job Information
Unifrax Value Stream Leader - Packing and Dry Processing in Derby, United Kingdom
Job Requirements
Why Work for Alkegen?
Alkegen brings together two of the world’s leading specialty materials companies to create one new, innovation-driven leader
focused on battery technologies, filtration media, and specialty insulation and sealing materials. Through global reach and
breakthrough inventions, we’re delivering products that enable the world to breathe easier, live greener, and go further than ever
before.
With over 60 manufacturing facilities with a global workforce of over 9,000 of the industry’s most experienced talent, including
insulation and filtration experts, Alkegen is uniquely positioned to help customers impact the environment in meaningful ways.
Alkegen offers a range of dynamic career opportunities with globe-spanning reach. From production operators to engineers,
technicians to specialists, sales to leadership, we’re always looking for top talent ready to bring their best. Come grow with us!
Main Purpose of Role
The Packing and Dry Processing Value Stream Leader plays a pivotal role in manufacturing operations. Responsible for overseeing packing and dry processing value stream including ensuring compliance with safety regulations, managing resources effectively, and addressing any operational issues promptly. This includes conducting disciplinary meetings when necessary and fostering a culture of continuous improvement within the manufacturing team. Additionally, this role is responsible for ensuring COSHH compliance, maintaining records of hazardous substances and ensuring employee safety. This position encompasses leading the team, optimising processes, and ensuring both productivity and well-being in the dry processing and packing value stream. This position will have overall responsibility for operators working across 3 shifts, supported by a Team Leader for the
afternoon shift.
Key Responsibilities
To ensure COSHH compliance, manage hazardous substance records, minimise exposure risks and address any COSHH issues promptly.
To partner with the Vacuum Forming Value Stream Leader to ensure the effective and efficient allocation of resources to ensure personal objectives and plant targets are consistently met.
To ensure any non-conforming product supplied from the vacuum forming value stream is reported to the Value Stream Leader and Quality Assistant.
To actively monitor performance across key performance indicators (KPI)
To ensure productivity is regularly reviewed and continually improved
To ensure timely execution of the packing priority list and ensure communication any issues to the Operations Planning and Operations Manager.
To ensure the box verification system is adhered to and maintained, raising any concerns immediately with the Quality Assistant and Operations Manager.
To support the maintenance of the plants ISO9001 quality management system and to ensure all products and materials are produced to the correct standards.
To ensure the timely and complete reporting of all breakdowns and improvement ideas via the plant maintenance and tooling ticket system, working with the Operations Manager to ensure the timely close out of relevant actions.
To ensure the adequate and timely stock and supply of spare tools, production supplies, raw materials, and personal protective equipment (PPE) to all operators.
To partner with the Operations Manager to deliver year on year increases in peakon survey participation rates and the successful implementation of any engagement plans.
To work with the wider plant team to foster a culture of continuous improvement and ongoing cost reduction which involves identifying and executing on opportunities for optimisation, cost reduction, productivity improvements.
To ensure all direct reports are adequately trained and equipped to perform their duties effectively.
Essential Qualifications and Experience
At least 5 years of experience in manufacturing leadership roles or positions
ILM Level 2 (or equivalent qualification)
IOSH Working Safely (or equivalent qualification)
Is able to demonstrate experience of working in a challenging environment with challenging individuals.
Demonstrates confidence, experience, and skill in building, leading, and motivating high-performing teams.
Demonstrates strong decision-making skills with a balance of analytical thinking and intuition.
Experience of working in a multi process manufacturing plant
Demonstrates experience of both working with and implementing 5S
Demonstrates a good understanding of lean manufacturing tools and techniques.
Can demonstrate expertise in identifying inefficiencies and implementing process and productivity improvements.
Good working knowledge of quality management systems e.g. ISO9001
Can clearly demonstrate an ability to analyse data, interpret metrics, and make informed decisions based on quantitative and qualitative information.
Demonstrates strong problem-solving skills with a systematic approach to identifying root causes and implementing effective solutions.
Demonstrated history of successful manufacturing supervision/management and tangible results in previous roles
Demonstrates exceptional organisation, time management and prioritisation skills.
Desirable Skills and Experience
Certified Six Sigma Green Belt Qualification
Batchelors degree in Manufacturing Engineering, Business Management, or closely related subject.
NEBOSH Certificate
ILM Level 5
Good understanding of production planning and control Key Result Areas
Peakon Survey Scores and Employee Engagement
Safety Incidents/Hazard Reporting and Closure
COSHH Compliance · Housekeeping Improvements / 5S Implementation
Training Plan Adherence
OEE Improvement
At Alkegen, we strive every day to help people – ALL PEOPLE – breathe easier, live greener and go further than ever before. We believe that diversity and inclusion is central to this mission and to our impact. Our diverse and inclusive culture drives our growth & innovation, and we nurture it by actively embracing our differences and using our varied perspectives to solve the complex challenges facing our changing and diverse world.
Employment selection and related decisions are made without regard to sex, race, ethnicity, nation of origin, religion, color, gender identity and expression, age, disability, education, opinions, culture, languages spoken, veteran’s status, or any other protected class.
Alkegen is a specialty materials leader serving mission-critical systems that the world is focused on for the future, including: battery technologies, electric vehicles, filtration media, and specialty insulation materials that enable customers to reduce fossil fuel consumption, save energy, and live greener.
We help people breathe easier, live greener, and go further than ever before.
Our experience speaks for itself. We are a vertically integrated manufacturer with the global reach and talent to solve your most demanding applications.
With 60 manufacturing facilities and 9,000+ highly skilled employees located around the world, we can solve any challenge.
Dedicated to sustainability and human health, we are uniquely positioned to help customers impact the environment in meaningful ways.